Aluminium pipes are essential components in various industries, including construction, automotive, and aerospace sectors. These pipes are highly sought-after for their lightweight yet durable properties, making them ideal for transporting fluids and gases. In UAE, aluminium pipes are manufactured and supplied by numerous companies, catering to diverse industrial needs. Whether for air conditioning systems, structural frameworks, or fluid transfer applications, aluminium pipes offer reliability and corrosion resistance. Their versatility extends to use in manufacturing aluminium tubes and round pipes, meeting specific requirements in different projects across the region. These qualities make aluminium pipes a preferred choice in modern engineering and construction.
Types of Aluminium Pipes
Aluminium pipes come in various types, each suited for different applications due to their specific characteristics:
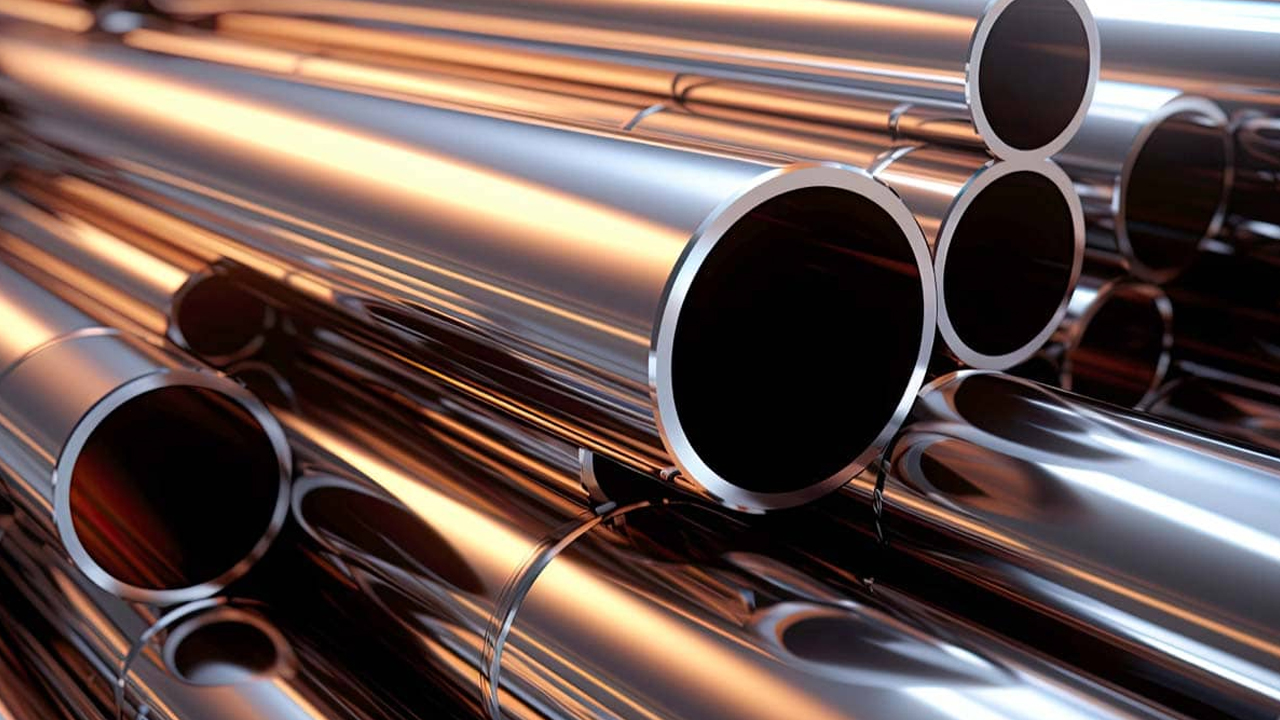
- • Aluminium Round Pipes: These are cylindrical pipes with a circular cross-section, commonly used in structural applications and fluid transport.
- • Aluminium Square Pipes: Featuring a square cross-section, these pipes are favored for architectural and framing purposes.
- • Aluminium Rectangular Pipes: Rectangular in shape, these pipes offer strength and stability, often used in construction and machinery.
- • Aluminium Seamless Pipes: These pipes are manufactured without any welding seams, ensuring high structural integrity and smooth internal surfaces.
- • Aluminium Welded Pipes: Constructed by welding aluminium sheets together, these pipes are cost-effective and suitable for general-purpose applications.
- • Aluminium Extruded Pipes: These are formed by forcing heated aluminium through a die, producing pipes with consistent dimensions and excellent surface finish.
- • Aluminium Alloy Pipes: Alloyed with other metals like zinc or magnesium, these pipes enhance strength and corrosion resistance, ideal for demanding environments.
Applications Across Industries
Aluminium pipes find diverse applications across various industries due to their versatile properties and structural advantages:
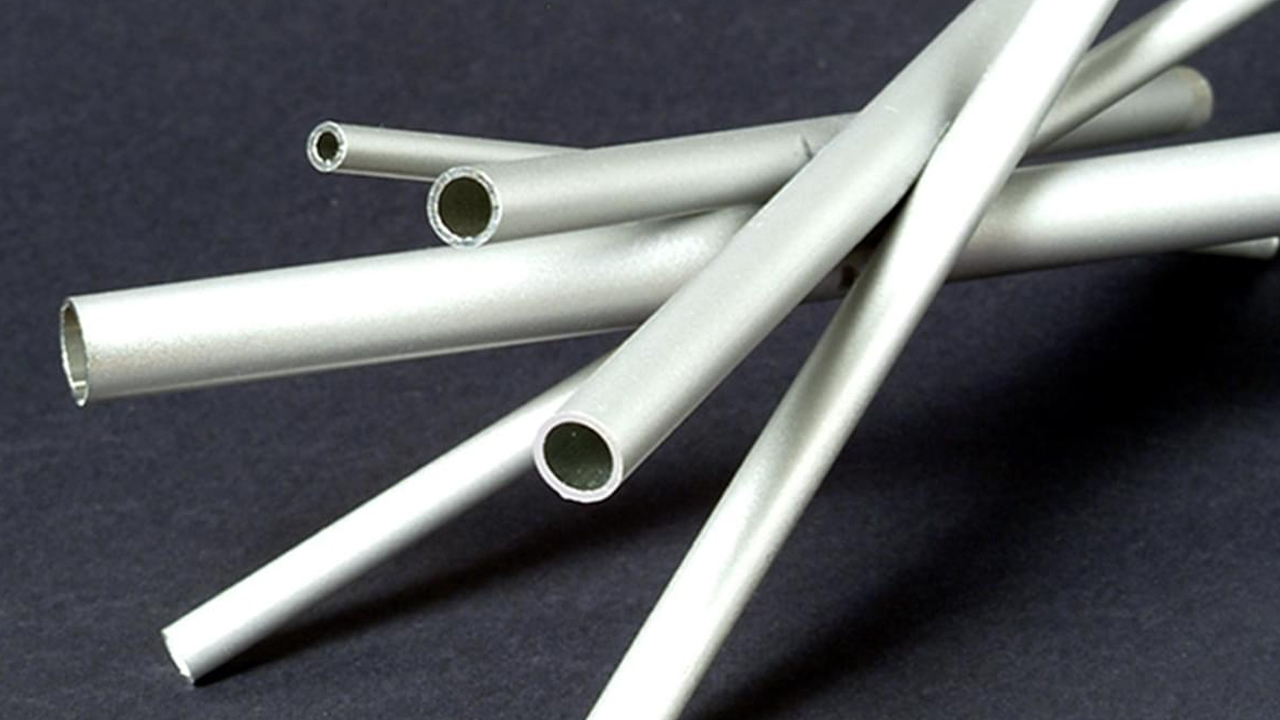
- • Construction Industry: Used in structural frameworks, scaffolding, and architectural elements due to their lightweight nature and corrosion resistance.
- • Automotive Sector: Employed for manufacturing radiator tubes, air intake systems, and exhaust pipes owing to their durability and heat transfer capabilities.
- • Aerospace and Aviation: Utilized in aircraft structures, fuel lines, and hydraulic systems due to their high strength-to-weight ratio and resistance to atmospheric corrosion.
- • Marine Applications: Ideal for boat hulls, masts, and piping systems due to their resistance to saltwater corrosion and lightweight properties.
- • Electrical Industry: Used for manufacturing electrical conduits and wiring due to their conductivity, non-magnetic properties, and ease of installation.
- • Manufacturing and Processing: Applied in manufacturing machinery, conveyor systems, and industrial piping for their durability and ease of machining.
- • Medical Sector: Used in equipment frames, support structures, and medical gas delivery systems due to their cleanliness, light weight, and resistance to corrosion.
Benefits of Aluminium Pipes
Aluminium pipes offer several benefits across various applications due to their unique properties and characteristics:
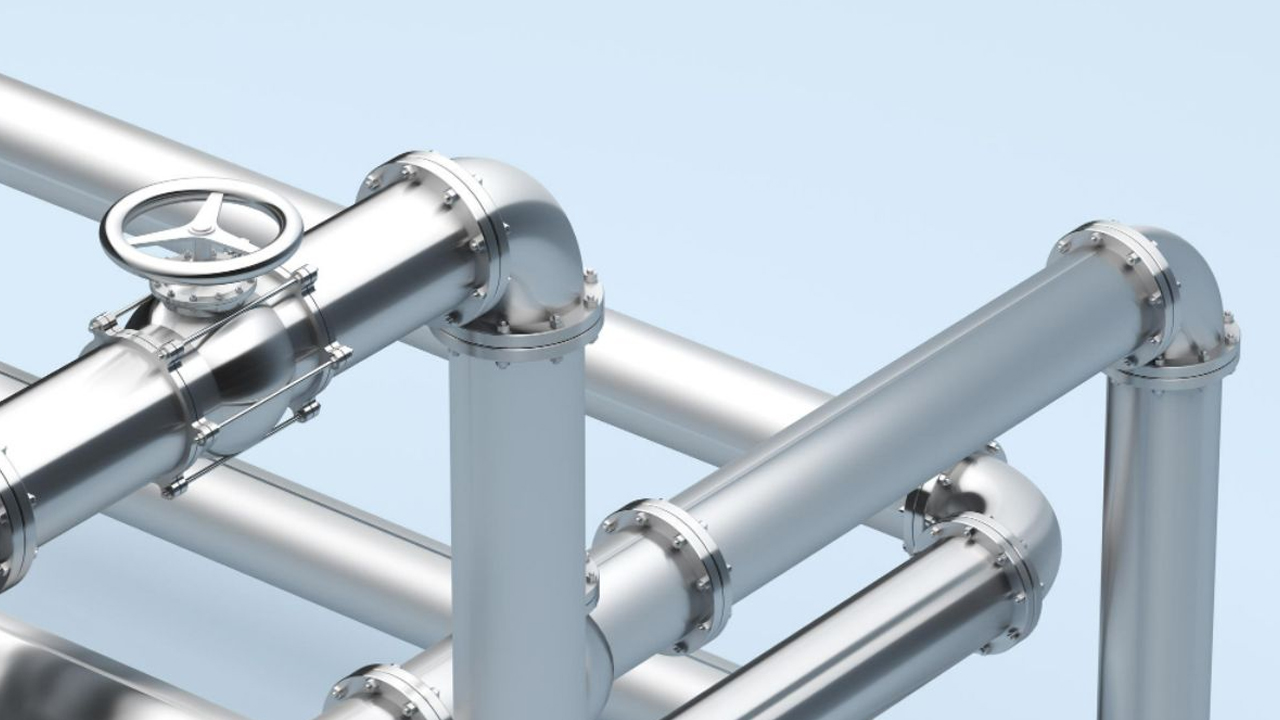
- • Lightweight: Aluminium pipes are lightweight, making them easy to handle, transport, and install compared to other metals like steel.
- • Corrosion Resistance: They have excellent corrosion resistance, particularly in marine and industrial environments, due to the formation of a protective oxide layer on the surface.
- • High Strength-to-Weight Ratio: Aluminium pipes provide strength comparable to steel but at a much lower weight, making them suitable for applications where weight reduction is critical.
- • Conductivity: They exhibit good thermal and electrical conductivity, making them ideal for applications in electrical wiring, heat exchangers, and other heat transfer equipment.
- • Ductility and Formability: Aluminium pipes are highly ductile and can be easily formed into various shapes and sizes, allowing for customization to meet specific design requirements.
- • Recyclability: Aluminium is fully recyclable without losing its inherent properties, making it a sustainable choice for environmentally-conscious projects.
- • Cost-Effective: They offer cost advantages in terms of material and transportation costs compared to other metals, especially in large-scale projects.
Overview Of The Manufacturing Processes Involved
The manufacturing of aluminium pipes involves several key processes to transform raw aluminium into finished pipes suitable for various applications:
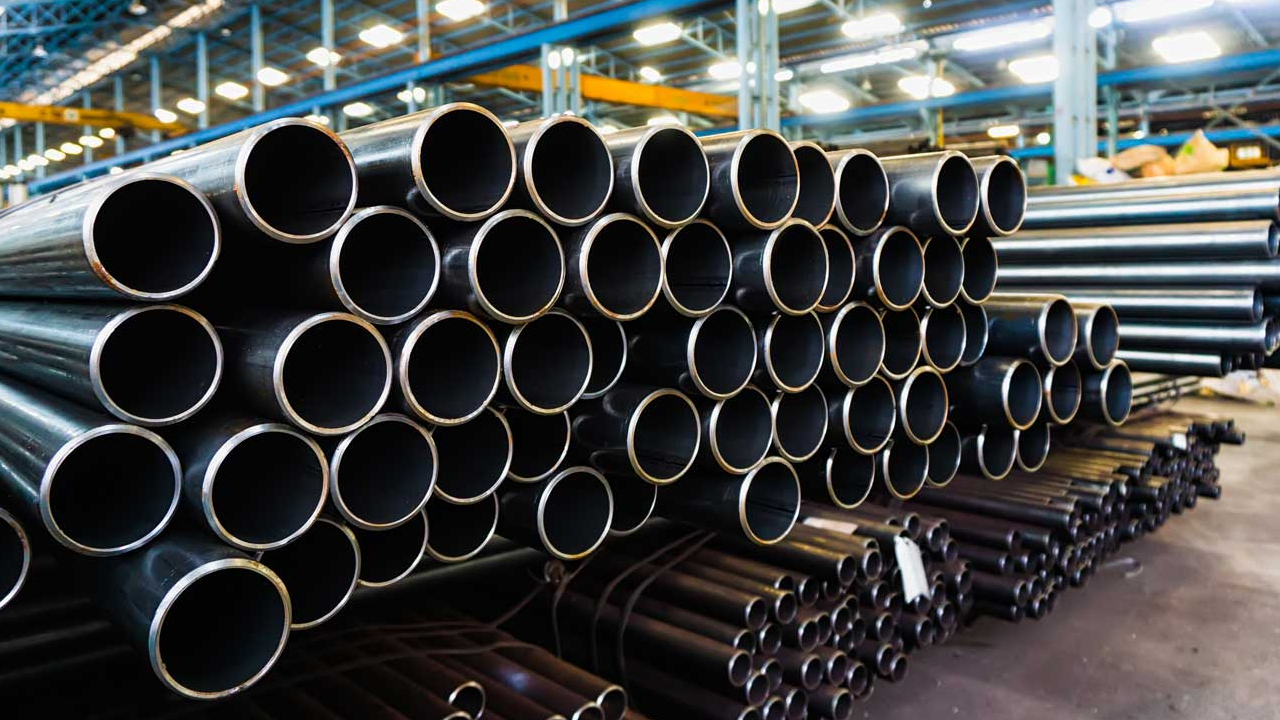
- • Extrusion: This is the primary method for manufacturing aluminium pipes. In extrusion, a heated aluminium billet is forced through a shaped die under high pressure to produce a continuous profile of the desired pipe shape. This process allows for complex cross-sections and consistent dimensions.
- • Drawing: Aluminium pipes can also be manufactured through drawing, where a solid aluminium rod or billet is pulled through a die to reduce its diameter and achieve the desired pipe size. This process is suitable for producing seamless pipes with precise dimensions.
- • Welding: Welded aluminium pipes are made by joining sections of aluminium using various welding techniques such as TIG (tungsten inert gas) welding or MIG (metal inert gas) welding. This method is used to create pipes of larger diameters or to join aluminium sections with complex shapes.
- • Cold Rolling: Cold rolling involves passing aluminium sheets or strips through a series of rollers at room temperature to reduce thickness and create long lengths of aluminium pipes. This process is particularly used for thin-walled pipes or where precise dimensional control is required.
- • Heat Treatment: After forming, aluminium pipes may undergo heat treatment processes such as annealing or tempering to improve their mechanical properties, enhance strength, or relieve internal stresses induced during manufacturing.
- • Surface Treatment: Aluminium pipes can be finished with various surface treatments such as anodizing, powder coating, or painting to enhance corrosion resistance, improve aesthetics, or meet specific application requirements.
Conclusion:
Aluminium pipes are crucial components across industries due to their lightweight nature, corrosion resistance, and versatility in various applications. The manufacturing processes such as extrusion, drawing, welding, cold rolling, heat treatment, and surface treatment ensure these pipes meet stringent quality standards. Their ability to withstand harsh environments while offering flexibility in design makes them ideal for construction, automotive, aerospace, and electronics sectors. With ongoing advancements in manufacturing technologies and materials, aluminium pipes continue to evolve, offering sustainable solutions and contributing to efficient, durable infrastructure worldwide.